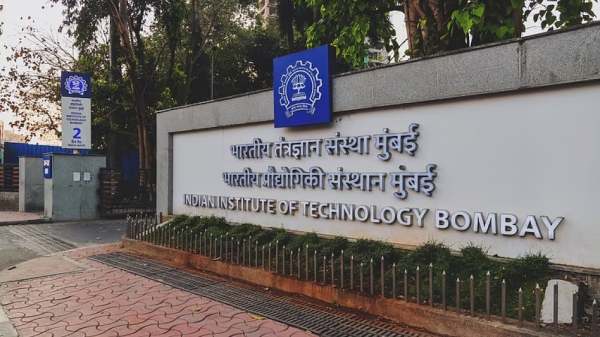
Mumbai: Researchers at the Indian Institute of Technology Bombay (IIT-B) have introduced a novel technique that significantly enhances the efficiency and strength of 3D metal printing. The innovation, termed "in-situ laser remelting”, allows for the production of denser and stronger structures at a rate 2.5 times faster than conventional methods.The study, led by PhD student Rajendra Hodgir under the guidance of Professors Ramesh Singh and Soham Mujumdar from the Department of Mechanical Engineering, addresses the persistent issue of structural defects in high-speed 3D metal printing. The team incorporated a crucial additional step in the printing process, wherein each printed layer is reheated with a laser before the next layer is added.“High deposition rates—printing a lot of material too quickly—often lead to defects such as porosities, cracks, and residual stresses,” explained Professor Mujumdar. “In some cases, large grains can weaken the overall structure. Smaller grains are usually preferred since their boundaries act as barriers to crack propagation, making the material stronger and tougher.”By remelting each layer immediately after deposition, the technique reduces porosity in the final product by 83%, improves surface smoothness by 59%, and enhances microhardness by 34%. Unlike other post-processing techniques, which require additional machinery and time-consuming treatments, this method operates seamlessly on existing 3D printing machines. “It’s happening on the same machine. You just turn off the powder and run the laser,” Mujumdar added.The research was conducted at the Machine Tools Lab in IIT-B using an experimental laser Directed Energy Deposition (L-DED) setup developed by Professor Singh’s group. The team determined that using a laser power of 2000 W and a scan speed of 400 mm/min produced the densest final structure in stainless steel (SS316L), a material widely used in aerospace, biomedical, and industrial applications.“The manufacturing sector is booming right now because of the government’s initiative to make everything in India,” Mujumdar noted. The researchers believe that their technique could strengthen India's self-reliance in advanced manufacturing, reducing dependence on imported high-precision components.Looking ahead, the team is refining the process to optimise efficiency further. Instead of remelting after every layer, they are investigating whether applying the technique every second or third layer can achieve similar benefits at a lower cost. Additionally, they are developing computational models to predict how different remelting parameters influence material properties, potentially enabling smarter and more optimised manufacturing processes.